Resources
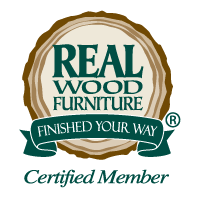
Certified retailers and manufacturers of Real Wood Furniture Finished Your Way® show a true commitment to quality craftsmanship. They know that the integrity of their furniture will be upheld for the long haul, if real wood is used throughout. Real Wood Furniture Finished Your Way® – Furniture craftsmanship that’s rooted in the past, manufactured for the present, and destined for the future!
Quality Create beautiful home furnishings! Solid woods can be repaired, sanded, or refinished. The majority of ready to finish furniture is made of solid wood. Wood has many advantages over particle board and chip board, which are predominant in the finished furniture industry. Wood expands and contracts depending on the humidity in the air. When constructed well, the natural expansion or contraction will cause no change in the item’s structural integrity. Finished furniture is typically a mix of real wood and particle board. As particle board does not expand and contract, but the wood does, the joints will eventually break from each other.
Product Knowledge When a piece is ready to finish, you can see what you are getting. Does the wood have knots, discoloration, obvious weak points or other defects? With finished furniture, you would not know until your new item began to fall apart. Ready to finish manufacturers must use a higher grade lumber in furniture production, because they can not “hide” such defects under a finish.
Value Purchasing a piece and finishing it yourself is less costly than purchasing a comparable, already finished piece of furniture. Your money buys you the best value for the dollar!
Flexibility You can purchase a single piece or an entire room. You can customize the finish and colors to match your décor. You can be creative, from a simple wood stain and varnish to a more elaborate stenciled or distressed finish. Stain it, paint it, make it yours!
Fun Finishing furniture can be a very enjoyable and relaxing hobby. It is easy to do. Just read the finishing instructions. There is a great sense of accomplishment and satisfaction that comes with finishing your own furniture.
What are the differences between hardwoods and softwoods?
Softwoods: In contrast, softwoods, or conifers, from the Latin word meaning “cone-bearing,” have needles. Widely available softwoods include cedar, fir, hemlock, pine, redwood and spruce.
Color: Very consistent in color – pale pinkish-brown to almost white.
Grain: No distinct grain pattern.
Characteristics: Good working properties, moderately lightweight, low shock resistance.
Finishing: Finishes smoothly and takes stain uniformly. Alder is a closed pore wood and requires minimal sanding. It may be finished to look like cherry, maple, walnut and other hardwoods.
Color: Nearly pure lustrous white, ranging through cream to very light brown.
Grain: It has an attractive, straight, moderately open, pronounced grain.
Characteristics: Heavy, hard, strong and stiff excellent bending qualities.
Finishing: Because of its large pores it is seldom painted but takes all other finishes very well.
Color: Very light and white in appearance.
Grain: Very even grained.
Finishing: Ideal for non-penetrating finishes such as water based stains and paints.
Color: Wood ranges from nearly white to deep red brown.
Grain: Close and straight grained, with little figure and a uniform texture, identified by its dark pores in conspicuous rays.
Characteristics: Hard and strong. Good resistance to abrasive wear.
Finishing: Easy to paint, stain or bleach.
Color: Cream or lightly tinged with red.
Grain: Fine grained (often curly or wavy).
Characteristics: Heavy, strong, hard, and even-textured.
Finishing: Birch takes paints and stains well.
Color: Rich, reddish-brown. Cherry darkens considerably with age and exposure to sunlight.
Grain: Straight-grained and satiny. Small gum pockets produce distinctive markings.
Characteristics: Light, strong, stiff and rather hard. Cherry’s grain is more subdued than some other hardwood species, with very interesting character.
Finishing: Cherry is unsurpassed in its finishing qualities-its uniform texture takes a finish very well.
Color: It is pinkish-brown in color and turns to a reddish-brown with age and exposure to light.
Characteristics: Its’ resistance to decay is relative to teak. Eucalyptus is a heavy hardwood that earns high marks for strength. Eucalyptus is a renewable resource with high productivity in relatively short harvest rotations. The wood in these products comes from well managed forests, independently certified in accordance with the rules of the Forest Stewardship Council (FSC).
Finishing: When finished with a high quality penetrating oil, mixed with the stain of your choice, Eucalyptus takes on a teak-like appearance. We recommend that you use one of the commercially available deck oils. To maintain a new look, occasionally clean and reseal the furniture. This furniture can be painted as well.
Color: White to tan to reddish-brown with inconspicuous fine brown lines.
Grain: Fine grain.
Characteristics: Extremely tough and resilient, even texture, quite hard and only moderately heavy.
Finishing: The grain pattern welcomes a full range of medium-to-dark finishes and bleaching treatments.
Color: Varies from light red or pale tan to a rich dark deep red or deep golden brown, depending on country of origin.
Grain: It is generally straight grained but is prized for its figures which include stripe, roe, curly, blister, fiddleback, and mottle.
Characteristics: Extremely strong, hard, stable and decay resistant.
Finishing: Finishes and stains to a beautiful natural luster.
Color: Cream to light reddish-brown.
Grain: Usually straight-grained and sometimes found with highly figured bird’s-eye or burl grain. Bird’s-eye resembles small circular or elliptical figures. Clusters of round curls are known as burl.
Characteristics: Heavy, hard, strong, tough, stiff, close-grained and possesses a uniform texture. Maple has excellent resistance to abrasion and indentation, making it ideal flooring as well as cutting boards and countertops.
Finishing: Takes stain satisfactorily and polishes well.
Color: White Oak- ranges from nearly white sapwood to a darker gray brown heartwood, Red Oak-ranges from nearly white cream color to a beautiful warm, pale brown heartwood, tinted with red.
Grain: The grain is distinguished by rays, which reflect light and add to its attractiveness. Depending on the way the logs are sawn into timber (rift-cut, flat sliced, flat sawn, rotary cut, quartered), many distinctive and sought after patterns emerge: flake figures, pin stripes, fine lines, leafy grains and watery figures.
Characteristics: Heavy, very strong and very hard, stiff, durable under exposure, great wear-resistance, holds nails and screws well.
Uses: Flooring, furniture, cabinets, ships and decorative woodwork.
Finishing: Oaks can be stained beautifully with a wide range of finish tones.
Color: Pale yellow.
Grain: Open grain similar to mahogany.
Characteristics: A very hard wood.
Finishing: Takes a very even stain.
Color: Pale cream color.
Grain: Has a distinctive grain pattern.
Finishing: Takes most finishes well.
Color: Warm pale yellow with brown knots.
Grain: Distinctive light and dark grain pattern.
Finishing: Pine takes most finishes well. End grain and spots that have been routed require extra sanding to prevent excessive penetration of stain. Knots in Pine furniture add color, interest and character; however they will “bleed” through washed or light finishes and they tend to darken with age. Always finish all surfaces including the bottom and inside with a clear coating of the finish coat. With some stains, a sealer helps prepare the wood to achieve a more even look.
Binder Finish or resin added to the stain, used to lock the pigment and dyes into the wood.
Blush Cloudy haze in finish caused by moisture trapped beneath the surface. High humidity is the most common cause. Can be also caused by the improper application of an oil base stain under a water base finish.
Coalescing The evaporation of the chemicals that keep the acrylic resin in a liquid form. Once this process is complete, the acrylic forms a hard finish film.
Crazing Tiny cracks in the finish film, usually along the edges of a surface. Caused by the finish drying too fast in high temperatures.
Extender Chemical additive used to control the drying and flow of water base finishes. Can be used with stains and finishes to “extend” the open time.
Fish Eyes Defects in the finish film caused by surface contamination (usually from oils, silicons, and waxes.)
Gloss The amount of light reflected off the finish surface. High gloss is rated 80-90°. Semi gloss is rated 50-75°. Satin is rated 30-45°. Rubbed effect is rated 20-25°. Flat sheen is rated 5-15°.
Grain Raising Tiny fibers in the wood grain that lift when exposed to water. Easily controlled with proper sanding.
HVLP (High Volume Low Pressure). An HVLP spray unit consists of a turbine motor that produces warm, low-pressure air. Its high transfer efficiency increases the square foot coverage.
Orange Peel Defect in finish film usually caused by cool drying temperatures or improper fluid tip size. The finish looks like the surface of an orange.
Pinholes Small defects in finish film caused by surface contamination. Resembles tiny holes in the finish.
Resin The material that forms a hard film on the surface after the chemicals have evaporated. Acrylics and urethanes are the common resins used in water base finishes.
Satin Finish that has had the gloss reduced to provide a softer sheen. A flattening agent made from fumed silica reduces the amount of light reflected by the surface.
Stain A liquid mixture to color wood. Made of 4 parts: Vehicle (water or solvent), Colorant (pigments and dyes), Binder (resin), Additives (solvents to control drying).
Viscosity The thickness of a fluid. This is used to determine flow rates for spray application. Usually measured with a #2 Zahn cup or #4 Ford cup. Viscosity can be decreased by using the appropriate thinner.
How do Hardwoods and Softwoods differ? They look different. Some are smooth, some have bold grain and some have knots or bird eyes. They finish differently. The density of the various woods change the depth and tone of the color. The region where the furniture is made, the style, and the historical period of the price determine the wood used.
Is Veneer less desirable than solid wood? Veneer has a different look than solid wood, but is not necessarily better or worse in quality. Veneer is a thin layer of wood applied in sheets over underlying layers of plywood. Originally developed to be an art form, veneer can be cut as thin as a dime and in intricate patterns. Uniform graining can be achieved, unlike the more random graining of solid wood.
When is plywood a good idea? When strength and stability are needed. Plywood is made of thin layers of sold wood glued over each other with grains running at 90-degree angles to produce a strong core. It is used to provide maximum stability on the sides of desks, entertainment centers and other units where solid woods would crack and warp. A veneer is often glued on top and sides for an even and attractive appearance.
Does price reflect quality? Yes. Just as with other commodities, the price of a piece of furniture increases when its quality improves. Higher prices reflect refinements in grades of wood and better construction features. The benefits to you: Less sanding and prepping work to finish.
Is furniture finishing hard to do? Using our step-by-step instructions, finishing is fun and easy. Match your existing décor or start fresh. With today’s finishing products, the possibilities are almost endless. Create your own style; express your individuality.
What supplies are needed, other than the stains? For most finishing projects, you will need a drop cloth, clean rags, paint brushes (bristle and foam), sandpaper or 3M sanding pads, q-tips and paper towels. If using oil-based finishes, have mineral spirits handy for cleanup.
Does the furniture require any assembly? Most items are fully assembled. There are some exceptions: Table legs and pedestals require attachment using the bolts provided; stools need to have the top swivel seat attached using the bolts provided; desks need to have the components attached to each other using the screws provided; since each bed frame has slightly different holes to attach the headboard, you do need to drill the holes and attach the headboard using the bolts provided. In all cases assembly is straightforward and simple.